Budowa maszyn pneumatycznych opiera się na kilku kluczowych elementach, które współpracują ze sobą, aby zapewnić efektywne działanie systemu. Wśród najważniejszych komponentów można wymienić sprężarki, które są odpowiedzialne za wytwarzanie sprężonego powietrza. Sprężarki mogą być różnego rodzaju, w tym tłokowe, śrubowe czy wirnikowe, a ich wybór zależy od specyfiki zastosowania. Kolejnym istotnym elementem są zbiorniki ciśnieniowe, które służą do przechowywania sprężonego powietrza i stabilizowania jego ciśnienia w systemie. Rury i przewody pneumatyczne stanowią niezbędną infrastrukturę do transportu sprężonego powietrza do poszczególnych urządzeń roboczych. Ważnym aspektem budowy maszyn pneumatycznych są również siłowniki pneumatyczne, które przekształcają energię sprężonego powietrza w ruch mechaniczny. Siłowniki te mogą mieć różne konstrukcje, takie jak cylindry jednostronnego lub dwustronnego działania, co wpływa na ich zastosowanie w różnych procesach technologicznych.
Jakie są zalety i wady maszyn pneumatycznych
Maszyny pneumatyczne cieszą się dużą popularnością w różnych branżach przemysłowych dzięki swoim licznym zaletom. Jedną z głównych korzyści jest ich prostota konstrukcji oraz łatwość w obsłudze. Dzięki temu operatorzy mogą szybko nauczyć się ich użycia, co przekłada się na efektywność pracy. Ponadto maszyny te charakteryzują się dużą niezawodnością oraz niskimi kosztami eksploatacyjnymi, ponieważ sprężone powietrze jest powszechnie dostępne i stosunkowo tanie. Dodatkowo maszyny pneumatyczne są często lżejsze od swoich elektrycznych odpowiedników, co ułatwia ich transport i instalację. Niemniej jednak istnieją także pewne wady związane z ich użytkowaniem. Wysoka cena zakupu niektórych komponentów oraz konieczność regularnej konserwacji mogą wpłynąć na całkowite koszty inwestycji. Ponadto wydajność maszyn pneumatycznych może być ograniczona przez zmiany temperatury oraz wilgotności powietrza, co może wpłynąć na stabilność pracy systemu.
Jakie zastosowania mają maszyny pneumatyczne w przemyśle
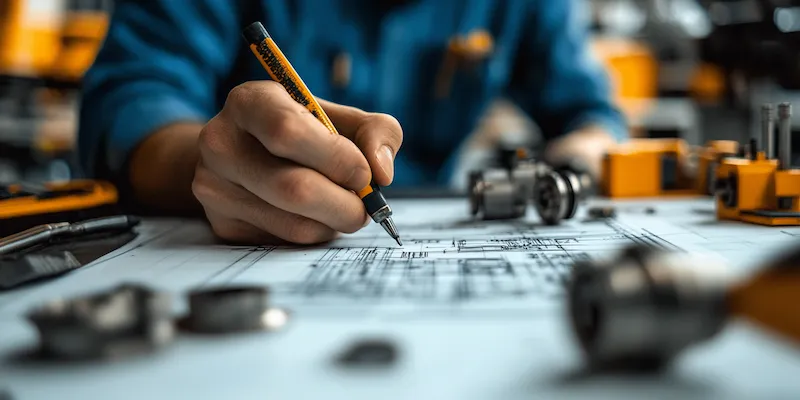
Maszyny pneumatyczne znajdują szerokie zastosowanie w różnych dziedzinach przemysłu, co czyni je niezwykle wszechstronnymi narzędziami. W przemyśle produkcyjnym są wykorzystywane do automatyzacji procesów montażowych oraz pakowania produktów. Dzięki swojej precyzji i szybkości działania maszyny te przyczyniają się do zwiększenia wydajności linii produkcyjnych. W branży budowlanej maszyny pneumatyczne są stosowane do narzędzi takich jak młoty udarowe czy wiertnice, które ułatwiają wykonywanie prac budowlanych i remontowych. W sektorze motoryzacyjnym maszyny te znajdują zastosowanie w procesach lakierniczych oraz montażowych, gdzie precyzyjne dozowanie materiałów jest kluczowe dla jakości końcowego produktu. Ponadto maszyny pneumatyczne odgrywają istotną rolę w logistyce i magazynowaniu, gdzie stosuje się je do podnoszenia i transportu ciężkich ładunków za pomocą siłowników pneumatycznych.
Jakie są nowoczesne technologie związane z maszynami pneumatycznymi
Nowoczesne technologie związane z maszynami pneumatycznymi stale ewoluują, co pozwala na zwiększenie efektywności oraz funkcjonalności tych urządzeń. Jednym z najważniejszych trendów jest rozwój systemów automatyki przemysłowej, które integrują maszyny pneumatyczne z nowoczesnymi rozwiązaniami informatycznymi. Dzięki temu możliwe jest zdalne monitorowanie pracy maszyn oraz optymalizacja procesów produkcyjnych poprzez analizę danych w czasie rzeczywistym. Innowacyjne rozwiązania obejmują także zastosowanie inteligentnych czujników ciśnienia i przepływu powietrza, które pozwalają na precyzyjne zarządzanie parametrami pracy systemu. Wprowadzenie technologii IoT (Internet of Things) umożliwia zdalne sterowanie maszynami oraz ich diagnostykę, co znacząco zwiększa bezpieczeństwo i komfort pracy operatorów. Kolejnym interesującym kierunkiem rozwoju jest wykorzystanie materiałów kompozytowych do budowy elementów maszyn pneumatycznych, co pozwala na redukcję ich masy przy jednoczesnym zachowaniu wysokiej wytrzymałości.
Jakie są najczęstsze problemy z maszynami pneumatycznymi
Maszyny pneumatyczne, mimo swojej niezawodności, mogą napotykać różnorodne problemy, które wpływają na ich wydajność i funkcjonalność. Jednym z najczęstszych problemów jest wyciek sprężonego powietrza, który może prowadzić do znacznych strat energii oraz obniżenia ciśnienia w systemie. Wyciek ten może być spowodowany uszkodzeniem przewodów, nieszczelności w połączeniach lub zużyciem uszczelek. Kolejnym istotnym problemem jest niewłaściwe działanie zaworów sterujących, które mogą prowadzić do nieprawidłowego przepływu powietrza i w konsekwencji do błędów w pracy maszyn. Zdarza się również, że siłowniki pneumatyczne ulegają awarii z powodu zanieczyszczeń w sprężonym powietrzu, co może prowadzić do ich zatarcia lub uszkodzenia. Warto także zwrócić uwagę na problemy związane z ciśnieniem roboczym; zbyt niskie ciśnienie może wpłynąć na wydajność maszyny, natomiast zbyt wysokie może prowadzić do uszkodzeń komponentów.
Jakie są różnice między maszynami pneumatycznymi a hydraulicznymi
Maszyny pneumatyczne i hydrauliczne to dwa różne systemy, które mają swoje unikalne cechy oraz zastosowania. Główna różnica między nimi polega na medium roboczym; maszyny pneumatyczne wykorzystują sprężone powietrze, podczas gdy maszyny hydrauliczne operują cieczą, najczęściej olejem hydraulicznym. Dzięki temu maszyny hydrauliczne mogą generować znacznie większe siły niż ich pneumatyczne odpowiedniki, co czyni je bardziej odpowiednimi do zastosowań wymagających dużej mocy, takich jak prasy czy dźwigi. Z drugiej strony maszyny pneumatyczne są zazwyczaj lżejsze i prostsze w budowie, co sprawia, że są łatwiejsze w obsłudze i konserwacji. Kolejną istotną różnicą jest szybkość działania; maszyny pneumatyczne charakteryzują się szybszym czasem reakcji i większą dynamiką ruchu, co czyni je idealnymi do zastosowań wymagających precyzyjnego sterowania ruchem. W kontekście kosztów eksploatacyjnych maszyny pneumatyczne mają tendencję do niższych kosztów operacyjnych ze względu na dostępność sprężonego powietrza oraz mniejsze wymagania dotyczące konserwacji.
Jakie są kluczowe zasady bezpieczeństwa przy pracy z maszynami pneumatycznymi
Bezpieczeństwo pracy z maszynami pneumatycznymi jest niezwykle ważne ze względu na potencjalne zagrożenia związane z używaniem sprężonego powietrza. Kluczową zasadą jest zawsze noszenie odpowiednich środków ochrony osobistej, takich jak gogle ochronne i rękawice, aby zminimalizować ryzyko obrażeń w przypadku awarii sprzętu lub wycieku sprężonego powietrza. Ważne jest również przeprowadzanie regularnych przeglądów technicznych maszyn oraz kontrola stanu przewodów i połączeń, aby wykrywać ewentualne nieszczelności czy uszkodzenia. Należy także przestrzegać zasad dotyczących ciśnienia roboczego; operatorzy powinni być świadomi maksymalnych wartości ciśnienia dla danego sprzętu oraz unikać przekraczania tych wartości. W przypadku pracy w grupie ważne jest stosowanie komunikacji między członkami zespołu oraz informowanie o wszelkich działaniach związanych z obsługą maszyn. Dodatkowo należy pamiętać o odpowiednim szkoleniu pracowników w zakresie obsługi maszyn pneumatycznych oraz procedur awaryjnych, co pozwoli na szybką reakcję w sytuacjach kryzysowych.
Jakie są przyszłe kierunki rozwoju technologii maszyn pneumatycznych
Przyszłość technologii związanej z maszynami pneumatycznymi zapowiada się obiecująco dzięki ciągłemu postępowi technologicznemu oraz rosnącym wymaganiom przemysłowym. Jednym z kluczowych kierunków rozwoju jest integracja sztucznej inteligencji oraz uczenia maszynowego w procesach zarządzania systemami pneumatycznymi. Dzięki tym technologiom możliwe będzie automatyczne dostosowywanie parametrów pracy maszyn do zmieniających się warunków produkcyjnych, co zwiększy ich efektywność i oszczędność energii. Kolejnym interesującym trendem jest rozwój materiałów kompozytowych oraz nanotechnologii, które mogą przyczynić się do stworzenia lżejszych i bardziej wytrzymałych komponentów maszyn pneumatycznych. Również ekologiczne podejście do projektowania urządzeń staje się coraz bardziej popularne; producenci starają się tworzyć maszyny o niższym zużyciu energii oraz mniejszej emisji hałasu. Wprowadzenie rozwiązań opartych na energii odnawialnej do systemów pneumatycznych również może stać się istotnym krokiem w kierunku zrównoważonego rozwoju przemysłu.
Jakie są koszty eksploatacji maszyn pneumatycznych
Koszty eksploatacji maszyn pneumatycznych mogą być różnorodne i zależą od wielu czynników, takich jak rodzaj urządzenia, jego zastosowanie oraz warunki pracy. Jednym z głównych kosztów jest energia potrzebna do wytwarzania sprężonego powietrza; koszty te mogą być znaczne, zwłaszcza jeśli sprężarki działają przez długi czas lub pracują pod dużym obciążeniem. Dodatkowo należy uwzględnić koszty konserwacji i naprawy sprzętu; regularne przeglądy techniczne oraz wymiana zużytych części są niezbędne dla zapewnienia długotrwałej efektywności działania maszyn. Koszty zakupu komponentów również mogą mieć duży wpływ na całkowite wydatki związane z eksploatacją systemu pneumatycznego; niektóre elementy mogą być drogie, zwłaszcza jeśli wymagają specjalistycznych materiałów lub technologii produkcji. Warto również pamiętać o kosztach związanych z szkoleniem pracowników; odpowiednie przeszkolenie personelu jest kluczowe dla bezpiecznej i efektywnej obsługi maszyn pneumatycznych.
Jakie są najnowsze innowacje w dziedzinie budowy maszyn pneumatycznych
Najnowsze innowacje w dziedzinie budowy maszyn pneumatycznych koncentrują się na poprawie wydajności oraz funkcjonalności tych urządzeń poprzez zastosowanie nowoczesnych technologii i materiałów. Jednym z ciekawszych osiągnięć jest rozwój inteligentnych systemów zarządzania sprężonym powietrzem, które pozwalają na optymalizację procesów produkcyjnych poprzez monitorowanie zużycia energii oraz automatyczne dostosowywanie parametrów pracy urządzeń. Innowacyjne rozwiązania obejmują także zastosowanie zaawansowanych czujników i aktuatorów, które umożliwiają precyzyjne sterowanie ruchem siłowników pneumatycznych oraz lepszą kontrolę nad procesami technologicznymi. Również materiały używane do produkcji elementów maszyn ulegają ciągłym udoskonaleniom; nowe kompozyty charakteryzujące się wysoką wytrzymałością i niską wagą pozwalają na budowę lżejszych i bardziej efektywnych urządzeń.