Budowa maszyn produkcyjnych to skomplikowany proces, który wymaga uwzględnienia wielu kluczowych elementów. W pierwszej kolejności należy zwrócić uwagę na konstrukcję mechaniczną, która stanowi podstawę funkcjonowania maszyny. Elementy te muszą być odpowiednio zaprojektowane, aby zapewnić stabilność i wytrzymałość w trakcie pracy. Kolejnym istotnym aspektem jest system napędowy, który odpowiada za ruch poszczególnych części maszyny. W zależności od przeznaczenia, może to być napęd elektryczny, hydrauliczny lub pneumatyczny. Ważne jest również zastosowanie odpowiednich materiałów, które będą odporne na zużycie oraz działanie różnych czynników zewnętrznych. Nie można zapominać o systemach sterowania, które umożliwiają precyzyjne zarządzanie pracą maszyny oraz jej parametrami.
Jakie technologie są wykorzystywane w budowie maszyn produkcyjnych
W dzisiejszych czasach budowa maszyn produkcyjnych opiera się na wielu nowoczesnych technologiach, które znacząco wpływają na ich wydajność i funkcjonalność. Jednym z najważniejszych trendów jest automatyzacja procesów produkcyjnych, która pozwala na zminimalizowanie błędów ludzkich oraz zwiększenie tempa pracy. W tym kontekście istotną rolę odgrywają roboty przemysłowe, które mogą wykonywać powtarzalne zadania z dużą precyzją. Ponadto, coraz częściej stosuje się technologie informacyjne i komunikacyjne do monitorowania i zarządzania procesami produkcyjnymi w czasie rzeczywistym. Dzięki temu możliwe jest szybkie reagowanie na wszelkie nieprawidłowości oraz optymalizacja pracy maszyn. Innowacyjne materiały kompozytowe oraz nanotechnologie również znajdują zastosowanie w budowie maszyn, co pozwala na uzyskanie lżejszych i bardziej wytrzymałych konstrukcji.
Jakie są najczęstsze problemy w budowie maszyn produkcyjnych
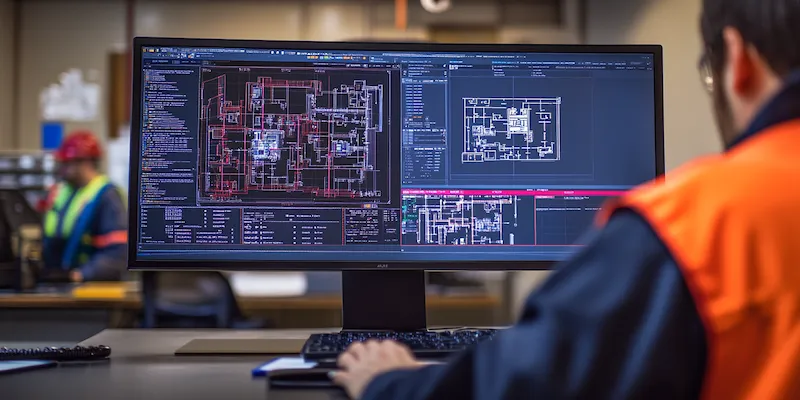
Budowa maszyn produkcyjnych wiąże się z wieloma wyzwaniami i problemami, które mogą wystąpić na różnych etapach procesu projektowania i realizacji. Jednym z najczęstszych problemów jest niewłaściwe dobranie materiałów do konstrukcji maszyny, co może prowadzić do szybkiego zużycia lub uszkodzeń w trakcie eksploatacji. Kolejnym istotnym zagadnieniem są błędy w projektowaniu systemu napędowego oraz mechanizmów roboczych, które mogą skutkować niską wydajnością lub nawet awariami maszyny. Problemy mogą również wynikać z braku odpowiedniej automatyzacji procesów, co prowadzi do większej liczby błędów ludzkich oraz spowolnienia produkcji. Niezbędne jest także zapewnienie właściwego szkolenia dla operatorów maszyn, ponieważ ich niewłaściwe użytkowanie może prowadzić do uszkodzeń sprzętu oraz zagrożeń dla bezpieczeństwa pracy.
Jakie są przyszłe kierunki rozwoju budowy maszyn produkcyjnych
Przyszłość budowy maszyn produkcyjnych zapowiada się niezwykle interesująco dzięki dynamicznemu rozwojowi technologii oraz zmieniającym się potrzebom rynku. W nadchodzących latach można spodziewać się dalszego wzrostu znaczenia automatyzacji i robotyzacji procesów produkcyjnych. Maszyny będą coraz bardziej zautomatyzowane, co pozwoli na osiągnięcie wyższej wydajności oraz redukcję kosztów operacyjnych. Równocześnie rozwój sztucznej inteligencji umożliwi lepsze zarządzanie procesami produkcyjnymi poprzez analizę danych oraz prognozowanie awarii. Warto również zwrócić uwagę na rosnącą popularność rozwiązań ekologicznych w budowie maszyn, takich jak wykorzystanie odnawialnych źródeł energii czy materiałów biodegradowalnych. Przemysł 4.0 staje się rzeczywistością, a integracja Internetu Rzeczy (IoT) z maszynami produkcyjnymi otworzy nowe możliwości w zakresie monitorowania i optymalizacji procesów.
Jakie są kluczowe aspekty projektowania maszyn produkcyjnych
Projektowanie maszyn produkcyjnych to proces, który wymaga uwzględnienia wielu kluczowych aspektów, aby zapewnić ich efektywność i niezawodność. Pierwszym krokiem w tym procesie jest dokładna analiza potrzeb użytkownika oraz specyfiki produkcji, co pozwala na stworzenie maszyny dostosowanej do konkretnych wymagań. Ważne jest również opracowanie odpowiednich schematów konstrukcyjnych oraz technologicznych, które będą stanowiły podstawę dla dalszych prac. W tym kontekście istotne jest wykorzystanie nowoczesnych narzędzi inżynieryjnych, takich jak programy CAD, które umożliwiają wizualizację projektu oraz symulację jego działania. Kolejnym kluczowym aspektem jest dobór odpowiednich komponentów, które muszą być nie tylko funkcjonalne, ale także kompatybilne z pozostałymi elementami maszyny. Niezwykle istotne jest również przeprowadzenie analizy kosztów, aby zapewnić rentowność inwestycji.
Jakie są kluczowe etapy budowy maszyn produkcyjnych
Budowa maszyn produkcyjnych składa się z kilku kluczowych etapów, które są niezbędne do uzyskania finalnego produktu o wysokiej jakości. Pierwszym etapem jest faza koncepcyjna, w której określane są cele projektowe oraz wymagania techniczne. W tym czasie inżynierowie i projektanci współpracują z klientami, aby zrozumieć ich potrzeby i oczekiwania. Następnie następuje faza projektowania, w której powstają szczegółowe rysunki techniczne oraz modele 3D maszyny. To moment, w którym wykorzystuje się zaawansowane oprogramowanie CAD do wizualizacji i symulacji działania maszyny w różnych warunkach. Po zakończeniu projektowania przechodzi się do etapu produkcji, który obejmuje wytwarzanie poszczególnych komponentów maszyny oraz ich montaż. W tym procesie niezwykle ważna jest precyzja oraz jakość wykonania, ponieważ błędy na tym etapie mogą prowadzić do poważnych problemów w późniejszej eksploatacji. Po zmontowaniu maszyny następuje jej testowanie, które ma na celu sprawdzenie funkcjonalności oraz wydajności.
Jakie są najważniejsze standardy jakości w budowie maszyn produkcyjnych
W budowie maszyn produkcyjnych niezwykle istotne jest przestrzeganie standardów jakości, które zapewniają bezpieczeństwo oraz efektywność działania sprzętu. Jednym z najważniejszych standardów jest norma ISO 9001, która dotyczy systemów zarządzania jakością. Organizacje, które wdrażają tę normę, muszą wykazać się zdolnością do dostarczania produktów spełniających wymagania klientów oraz przepisów prawnych. Kolejnym istotnym standardem jest ISO 14001, który koncentruje się na zarządzaniu środowiskowym i ma na celu minimalizację negatywnego wpływu działalności przemysłowej na środowisko naturalne. W przypadku maszyn produkcyjnych ważne są również normy dotyczące bezpieczeństwa pracy, takie jak dyrektywa maszynowa Unii Europejskiej, która określa wymagania dotyczące konstrukcji i użytkowania maszyn w celu ochrony zdrowia pracowników. Dodatkowo wiele firm stosuje wewnętrzne procedury kontrolne oraz audyty jakościowe, aby zapewnić zgodność z obowiązującymi normami i standardami.
Jakie są wyzwania związane z modernizacją maszyn produkcyjnych
Modernizacja maszyn produkcyjnych to proces, który niesie ze sobą wiele wyzwań i trudności. Jednym z głównych problemów jest konieczność dostosowania starszych modeli do nowoczesnych technologii bez konieczności całkowitej wymiany sprzętu. Wiele firm boryka się z ograniczeniami finansowymi, które mogą utrudniać realizację ambitnych planów modernizacyjnych. Kolejnym wyzwaniem jest integracja nowych systemów automatyzacji z istniejącymi rozwiązaniami technologicznymi, co często wymaga zaawansowanej wiedzy inżynieryjnej oraz doświadczenia w zakresie programowania i konfiguracji urządzeń. Istotnym aspektem jest również szkolenie personelu, ponieważ nowoczesne technologie mogą być skomplikowane i wymagają odpowiednich umiejętności od operatorów maszyn. Dodatkowo modernizacja może wiązać się z przestojami w produkcji, co generuje dodatkowe koszty dla przedsiębiorstwa. Ważne jest więc staranne planowanie procesu modernizacji oraz analiza potencjalnych korzyści płynących z inwestycji w nowe technologie.
Jakie są zalety stosowania nowoczesnych materiałów w budowie maszyn produkcyjnych
Stosowanie nowoczesnych materiałów w budowie maszyn produkcyjnych przynosi szereg korzyści, które mają istotny wpływ na wydajność i trwałość sprzętu. Nowoczesne materiały kompozytowe charakteryzują się niską wagą przy jednoczesnej wysokiej wytrzymałości, co pozwala na redukcję masy maszyny oraz zwiększenie jej efektywności energetycznej. Dzięki zastosowaniu takich materiałów możliwe jest również uzyskanie lepszej odporności na korozję oraz działanie czynników chemicznych, co przekłada się na dłuższy okres eksploatacji sprzętu. Ponadto innowacyjne materiały mogą być projektowane tak, aby spełniały specyficzne wymagania dotyczące przewodnictwa cieplnego czy elektrycznego, co otwiera nowe możliwości w zakresie konstrukcji maszyn. Zastosowanie nanotechnologii pozwala na tworzenie powierzchni o specjalnych właściwościach, takich jak zwiększona odporność na zużycie czy samoczyszczące się powierzchnie. Warto również zwrócić uwagę na aspekty ekologiczne – wiele nowoczesnych materiałów można poddać recyklingowi lub są one biodegradowalne, co wpisuje się w trend zrównoważonego rozwoju przemysłu.
Jakie są różnice między maszynami produkcyjnymi a innymi rodzajami maszyn
Maszyny produkcyjne różnią się od innych rodzajów maszyn przede wszystkim swoim przeznaczeniem oraz funkcjonalnością. Głównym celem maszyn produkcyjnych jest wspieranie procesów wytwórczych poprzez automatyzację działań związanych z obróbką materiałów lub montażem produktów. W przeciwieństwie do nich maszyny używane w innych branżach mogą mieć różnorodne zastosowania – od transportu po pakowanie czy magazynowanie towarów. Maszyny produkcyjne często charakteryzują się dużą wydajnością oraz zdolnością do pracy w trybie ciągłym przez długie okresy czasu bez przestojów. Wiele z nich wyposażonych jest w zaawansowane systemy sterowania i monitorowania, co pozwala na precyzyjne zarządzanie procesem produkcji oraz szybką reakcję na ewentualne problemy. Różnice te obejmują również konstrukcję mechaniczną – maszyny produkcyjne muszą być bardziej wytrzymałe i odporne na intensywne użytkowanie niż inne rodzaje sprzętu.
Jakie są kluczowe czynniki wpływające na koszt budowy maszyn produkcyjnych
Koszt budowy maszyn produkcyjnych zależy od wielu kluczowych czynników, które należy uwzględnić już na etapie planowania projektu. Pierwszym czynnikiem jest wybór technologii i komponentów – nowoczesne rozwiązania często wiążą się z wyższymi kosztami zakupu, jednak mogą przynieść oszczędności w dłuższej perspektywie dzięki zwiększonej wydajności i mniejszym kosztom eksploatacyjnym. Kolejnym istotnym aspektem są koszty pracy związane z projektowaniem i montażem maszyny; wysoko wykwalifikowani specjaliści mogą znacząco podnieść całkowity koszt inwestycji. Należy również uwzględnić koszty związane z testowaniem oraz certyfikacją maszyny zgodnie z obowiązującymi normami jakości i bezpieczeństwa. Dodatkowo lokalizacja zakładu produkcyjnego może wpłynąć na koszty transportu komponentów oraz dostępność surowców potrzebnych do budowy maszyny.