Destylacja rozpuszczalników to proces, który polega na oddzieleniu substancji na podstawie różnicy w ich temperaturach wrzenia. Jest to technika szeroko stosowana w chemii oraz przemyśle, umożliwiająca oczyszczanie cieczy oraz odzyskiwanie rozpuszczalników. Proces ten rozpoczyna się od podgrzewania mieszanki, co prowadzi do odparowania składników o niższej temperaturze wrzenia. Opary te następnie skraplają się w chłodnicy, tworząc czystą ciecz, która jest zbierana jako destylat. Kluczowym elementem tego procesu jest wybór odpowiedniego sprzętu, takiego jak kolumna destylacyjna czy alembik, które wpływają na efektywność separacji. Warto również zwrócić uwagę na czystość używanych surowców, ponieważ zanieczyszczenia mogą wpłynąć na jakość końcowego produktu.
Jakie są różne metody destylacji rozpuszczalników
W kontekście destylacji rozpuszczalników istnieje kilka różnych metod, które można zastosować w zależności od specyfiki procesu oraz rodzaju substancji. Najpopularniejszą metodą jest destylacja prosta, która sprawdza się w przypadku substancji o znacznej różnicy temperatur wrzenia. W sytuacjach, gdy różnice te są niewielkie, lepszym rozwiązaniem może być destylacja frakcyjna. Ta metoda polega na wielokrotnym skraplaniu i odparowywaniu oparów, co pozwala na uzyskanie wyższej czystości końcowego produktu. Inną techniką jest destylacja azeotropowa, która wykorzystuje dodatki chemiczne do zmiany właściwości mieszaniny i umożliwienia separacji składników. Warto również wspomnieć o destylacji pod ciśnieniem atmosferycznym oraz pod próżnią, które mają zastosowanie w przypadku substancji wrażliwych na wysoką temperaturę.
Jakie są zastosowania destylacji rozpuszczalników w przemyśle
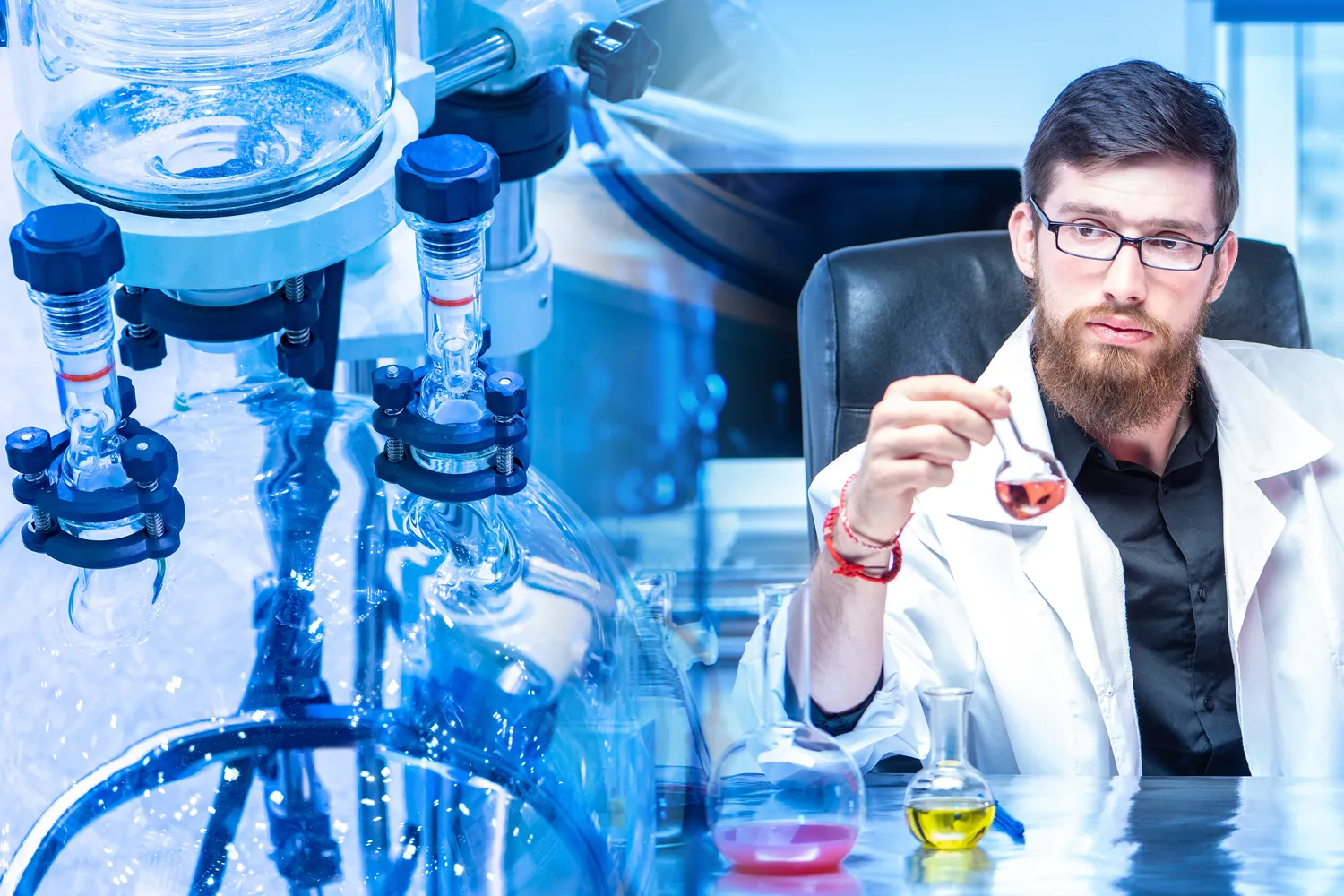
Destylacja rozpuszczalników znajduje szerokie zastosowanie w różnych dziedzinach przemysłu, co czyni ją kluczowym procesem technologicznym. W przemyśle chemicznym jest wykorzystywana do oczyszczania surowców oraz produkcji wysokiej jakości substancji chemicznych. Na przykład w produkcji alkoholi etylowych destylacja pozwala na uzyskanie czystego produktu poprzez usunięcie zanieczyszczeń i niepożądanych składników. W przemyśle farmaceutycznym proces ten jest niezbędny do produkcji leków o wysokiej czystości, gdzie nawet najmniejsze zanieczyszczenia mogą wpłynąć na skuteczność terapii. Ponadto destylacja rozpuszczalników jest istotna w branży petrochemicznej, gdzie służy do separacji różnych frakcji ropy naftowej, takich jak benzyna czy olej napędowy. Warto również zauważyć, że proces ten może być stosowany do recyklingu rozpuszczalników organicznych, co przyczynia się do ochrony środowiska poprzez zmniejszenie ilości odpadów chemicznych oraz oszczędność surowców naturalnych.
Jakie są najważniejsze czynniki wpływające na efektywność destylacji
Efektywność procesu destylacji rozpuszczalników zależy od wielu czynników, które mogą znacząco wpłynąć na jakość uzyskanego produktu oraz wydajność całego procesu. Jednym z najważniejszych aspektów jest temperatura wrzenia poszczególnych składników mieszanki. Im większa różnica temperatur wrzenia między składnikami, tym łatwiejsze jest ich oddzielenie. Kolejnym kluczowym czynnikiem jest ciśnienie atmosferyczne; obniżenie ciśnienia może umożliwić destylację substancji wrażliwych na wysoką temperaturę bez ryzyka ich degradacji. Ważne jest także odpowiednie dobranie sprzętu do przeprowadzania procesu; kolumny destylacyjne o dużej powierzchni wymiany ciepła mogą znacznie zwiększyć efektywność separacji. Również czas trwania procesu ma znaczenie; zbyt krótki czas może prowadzić do niedostatecznej separacji składników, podczas gdy zbyt długi czas może skutkować stratami materiałowymi oraz obniżeniem jakości produktu końcowego.
Jakie są najczęstsze problemy podczas destylacji rozpuszczalników
Podczas procesu destylacji rozpuszczalników mogą wystąpić różnorodne problemy, które wpływają na jakość i wydajność końcowego produktu. Jednym z najczęstszych problemów jest tworzenie się azeotropów, czyli mieszanin, które mają stały skład i nie można ich oddzielić za pomocą standardowej destylacji. Azeotropy mogą prowadzić do trudności w uzyskaniu czystych składników, co jest szczególnie problematyczne w przypadku substancji o podobnych temperaturach wrzenia. Innym istotnym problemem jest zanieczyszczenie destylatu, które może być spowodowane niewłaściwym doborem materiałów lub sprzętu. Zanieczyszczenia te mogą pochodzić z surowców, a także z samego procesu, jeśli nie są zachowane odpowiednie standardy czystości. Dodatkowo, niewłaściwe ustawienia temperatury i ciśnienia mogą prowadzić do nieefektywnej separacji składników oraz strat materiałowych. Warto również zwrócić uwagę na ryzyko przegrzania lub niedogrzania kolumny destylacyjnej, co może skutkować nieprawidłowym przebiegiem procesu.
Jakie są różnice między destylacją a innymi metodami separacji
Destylacja rozpuszczalników jest jedną z wielu metod separacji substancji chemicznych, ale różni się od innych technik pod względem zasad działania oraz zastosowań. Na przykład, w przeciwieństwie do ekstrakcji, która polega na wykorzystaniu rozpuszczalnika do wydobywania składników z mieszanki, destylacja opiera się na różnicach w temperaturach wrzenia. Ekstrakcja może być bardziej efektywna w przypadku substancji o niskich temperaturach wrzenia lub w sytuacjach, gdy składniki są bardzo rozpuszczalne w danym rozpuszczalniku. Inną popularną metodą separacji jest filtracja, która polega na oddzieleniu ciał stałych od cieczy za pomocą porowatego materiału. Filtracja jest skuteczna w przypadku mieszanin stałych i ciekłych, ale nie sprawdza się w przypadku cieczy o podobnych właściwościach fizykochemicznych. Również chromatografia to technika separacyjna, która pozwala na oddzielanie składników na podstawie ich interakcji z fazą stacjonarną i ruchomą. Choć chromatografia często zapewnia wyższą czystość niż destylacja, jest zazwyczaj bardziej czasochłonna i kosztowna.
Jakie są nowoczesne technologie stosowane w destylacji
W ostatnich latach rozwój technologii przyczynił się do znacznych ulepszeń w procesie destylacji rozpuszczalników. Nowoczesne kolumny destylacyjne wyposażone są w zaawansowane systemy kontroli temperatury i ciśnienia, co pozwala na precyzyjne dostosowanie warunków pracy do specyfiki przetwarzanej mieszanki. Wprowadzenie automatyzacji do procesów destylacyjnych umożliwia ciągłe monitorowanie parametrów oraz szybszą reakcję na ewentualne problemy. Ponadto rozwój materiałów budowlanych kolumn i chłodnic przyczynił się do zwiększenia efektywności energetycznej procesów destylacyjnych. Coraz częściej stosuje się również technologie membranowe jako alternatywę dla tradycyjnej destylacji; membrany pozwalają na selektywne oddzielanie składników na podstawie ich wielkości lub właściwości chemicznych. Innowacyjne podejścia obejmują także zastosowanie nanotechnologii oraz biotechnologii w procesach separacyjnych, co otwiera nowe możliwości dla przemysłu chemicznego i farmaceutycznego.
Jakie są aspekty ekologiczne związane z destylacją rozpuszczalników
Aspekty ekologiczne związane z destylacją rozpuszczalników stają się coraz ważniejsze w kontekście globalnych wyzwań związanych z ochroną środowiska. Proces ten często wiąże się z wysokim zużyciem energii, co przyczynia się do emisji gazów cieplarnianych oraz innych substancji szkodliwych dla atmosfery. Dlatego wiele firm poszukuje sposobów na optymalizację procesów destylacyjnych w celu zmniejszenia ich wpływu na środowisko. Jednym z podejść jest wdrażanie technologii odzysku ciepła, które pozwalają na ponowne wykorzystanie energii generowanej podczas procesu destylacji. Ponadto recykling rozpuszczalników staje się coraz bardziej popularny; dzięki temu możliwe jest ograniczenie ilości odpadów chemicznych oraz zmniejszenie zapotrzebowania na nowe surowce. Warto również zwrócić uwagę na rozwój bioprospekcji i poszukiwanie naturalnych substancji chemicznych jako alternatywy dla syntetycznych rozpuszczalników, co może przyczynić się do zmniejszenia negatywnego wpływu przemysłu chemicznego na środowisko naturalne.
Jakie są przyszłe kierunki badań nad destylacją rozpuszczalników
Przyszłość badań nad destylacją rozpuszczalników zapowiada się obiecująco dzięki rosnącemu zainteresowaniu nowymi technologiami oraz ekologicznymi rozwiązaniami. Naukowcy koncentrują się na opracowywaniu bardziej efektywnych metod separacji, które mogłyby zastąpić tradycyjne techniki destylacyjne. Badania nad wykorzystaniem nanomateriałów oraz zaawansowanych membran otwierają nowe możliwości dla procesów separacyjnych, które mogą być bardziej energooszczędne i mniej szkodliwe dla środowiska. Ponadto rozwój sztucznej inteligencji i uczenia maszynowego może przyczynić się do optymalizacji procesów produkcyjnych poprzez lepsze przewidywanie zachowań różnych substancji podczas destylacji. W kontekście zmian klimatycznych coraz większą uwagę przykłada się także do badań nad redukcją emisji gazów cieplarnianych związanych z procesami przemysłowymi, co może wpłynąć na przyszłe regulacje prawne dotyczące przemysłu chemicznego.
Jakie są kluczowe wyzwania w rozwoju destylacji rozpuszczalników
Rozwój technologii destylacji rozpuszczalników wiąże się z wieloma kluczowymi wyzwaniami, które muszą zostać pokonane, aby procesy te mogły stać się bardziej efektywne i ekologiczne. Jednym z głównych wyzwań jest konieczność zmniejszenia zużycia energii, co jest szczególnie istotne w kontekście globalnych wysiłków na rzecz zrównoważonego rozwoju. Wysokie koszty operacyjne związane z energią mogą ograniczać konkurencyjność procesów destylacyjnych w porównaniu do alternatywnych metod separacji. Dodatkowo, rozwój nowych materiałów i technologii wymaga znacznych inwestycji oraz badań, co może być barierą dla wielu przedsiębiorstw. Kolejnym wyzwaniem jest zapewnienie wysokiej jakości produktów końcowych, co wymaga ciągłego doskonalenia procesów oraz monitorowania jakości surowców. Wreszcie, zmieniające się regulacje prawne dotyczące ochrony środowiska oraz bezpieczeństwa chemicznego mogą wpływać na sposób prowadzenia procesów destylacyjnych, co wymaga elastyczności i innowacyjności ze strony przemysłu.